The 5-Minute Rule for Alcast Company
The 5-Minute Rule for Alcast Company
Blog Article
Alcast Company Things To Know Before You Get This
Table of ContentsAlcast Company Can Be Fun For AnyoneThe 30-Second Trick For Alcast CompanyThe smart Trick of Alcast Company That Nobody is Talking About9 Simple Techniques For Alcast CompanyFacts About Alcast Company UncoveredThe Best Strategy To Use For Alcast Company
The subtle distinction exists in the chemical material. Chemical Contrast of Cast Light weight aluminum Alloys Silicon promotes castability by lowering the alloy's melting temperature level and enhancing fluidity throughout spreading. It plays a vital function in enabling complex molds to be filled up precisely. Furthermore, silicon adds to the alloy's toughness and put on resistance, making it useful in applications where longevity is vital, such as automobile parts and engine parts.It also enhances the machinability of the alloy, making it much easier to refine into ended up items. By doing this, iron contributes to the total workability of aluminum alloys. Copper enhances electric conductivity, making it advantageous in electric applications. It additionally boosts deterioration resistance and contributes to the alloy's overall stamina.
Manganese adds to the stamina of aluminum alloys and improves workability (Aluminum Castings). It is typically used in functioned light weight aluminum products like sheets, extrusions, and accounts. The visibility of manganese help in the alloy's formability and resistance to splitting during fabrication procedures. Magnesium is a lightweight aspect that provides strength and impact resistance to aluminum alloys.
The smart Trick of Alcast Company That Nobody is Talking About
Zinc enhances the castability of light weight aluminum alloys and helps control the solidification procedure throughout casting. It enhances the alloy's stamina and solidity.
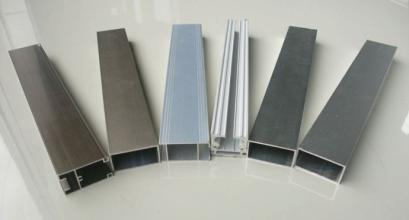
The primary thermal conductivity, tensile toughness, yield stamina, and elongation vary. Select ideal basic materials according to the efficiency of the target product generated. Amongst the above alloys, A356 has the greatest thermal conductivity, and A380 and ADC12 have the most affordable. The tensile restriction is the contrary. A360 has the most effective return strength and the highest prolongation price.
Everything about Alcast Company

In accuracy spreading, 6063 is appropriate for applications where detailed geometries and high-quality surface coatings are paramount. Examples consist of telecommunication rooms, where the alloy's superior formability enables smooth and aesthetically pleasing layouts while maintaining structural honesty. Similarly, in the Lights Solutions industry, precision-cast 6063 components produce sophisticated and efficient lights fixtures that require complex shapes and excellent thermal performance.
It brings about a finer surface area coating and much better deterioration resistance in A360. Moreover, the A360 displays superior elongation, making it optimal for facility and thin-walled parts. In accuracy casting applications, A360 is appropriate for markets such as Consumer Electronic Devices, Telecommunication, and Power Devices. Its improved fluidness permits elaborate, high-precision components like smartphone casings and communication gadget real estates.
The Basic Principles Of Alcast Company
Its unique residential properties make A360 an important choice for accuracy spreading in these industries, enhancing item durability and high quality. Aluminum alloy 380, or A380, is an extensively made use of casting alloy with several distinct features. It supplies exceptional castability, making it a perfect selection for accuracy casting. A380 exhibits great fluidity when molten, making certain complex and comprehensive molds are properly replicated.
In accuracy spreading, light weight aluminum 413 beams in the Customer Electronics and Power Tools industries. This alloy's exceptional deterioration resistance makes it a superb selection for outside applications, making certain long-lasting, durable products in the discussed markets.
Alcast Company Fundamentals Explained
Once you have made a decision that the light weight aluminum pass away casting procedure appropriates for your project, an essential next action is picking one of the most suitable alloy. The light weight aluminum alloy you choose will considerably affect both the casting process more and the homes of the end product. As a result of this, you must make your decision carefully and take an informed strategy.
Establishing the most suitable light weight aluminum alloy for your application will mean considering a wide selection of characteristics. The initial group addresses alloy attributes that impact the production procedure.
Alcast Company for Dummies
The alloy you choose for die casting straight impacts several aspects of the casting procedure, like how simple the alloy is to work with and if it is prone to casting defects. Hot fracturing, likewise called solidification splitting, is a regular die casting defect for aluminum alloys that can cause interior or surface-level splits or splits.
Certain aluminum alloys are extra susceptible to hot fracturing than others, and your option needs to consider this. One more typical flaw discovered in the die casting of light weight aluminum is pass away soldering, which is when the actors stays with the die walls and makes ejection hard. It can damage both the cast and the die, so you ought to look for alloys with high anti-soldering residential or commercial properties.
Rust resistance, which is currently a noteworthy feature of aluminum, can vary significantly from alloy to alloy and is an important particular to consider relying on the environmental conditions your product will be subjected to (Aluminum Casting). Use resistance is another residential or commercial property frequently sought in aluminum items and can distinguish some alloys
Report this page